Goleta aluminum company plays vital role in global ventilator production
GOLETA, Calif. - Worldwide demand for life-saving ventilators is having a major impact on an industrial engineering company in Goleta specializing in aluminum.
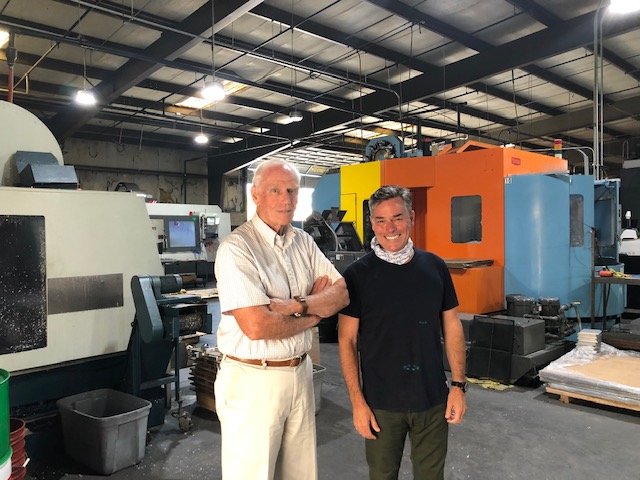
"My grandfather started the company in 1945," said Alex Rasmussen, President and CEO of Neal Feay Co. "He worked building planes during the war and was thinking about, 'What's going to happen post World War II?'"
Rasmussen credits his grandfather's vision to anodize and colorize the malleable metal and eventually branch out the company into design and manufacturing.
"He really rode that wave of the Eames and Noguchi's," Rasmussen said. "He started with all his own little gift items, smoking accessories. It was the 40's. And then, a woman's cuff was a big success."
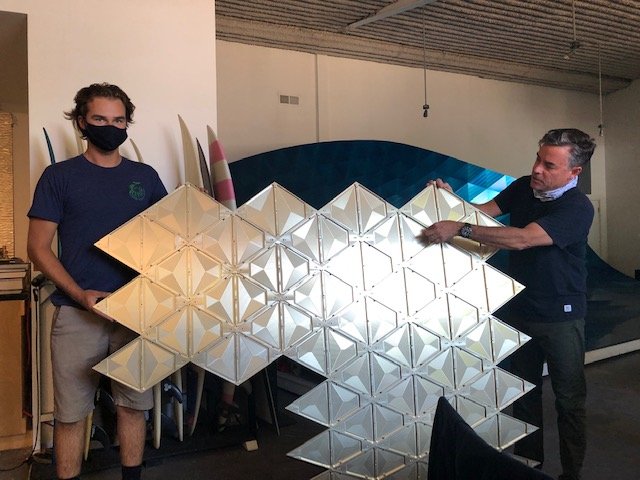
Rasmussen's father, Neal, was 9-years-old at the time. Decades later, he took over the reigns.
"He was raised in the company and I was really, really raised in the company," Rasmussen said with a laugh. "Then, my mom was an art major so I'm what happens if you're raised in the factory and your mom is an art major."
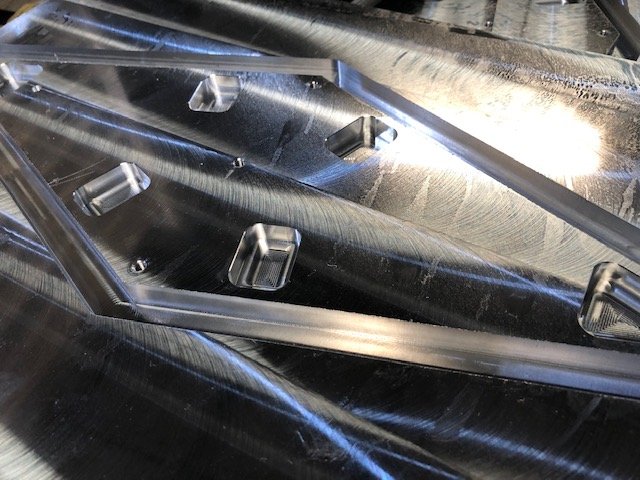
Over time, Neal Feay Co became a global, high quality supplier and now ranks among the top go-to businesses for anodized aluminum based products and artwork.
"We were doing a large project for a big French luxury brand and then doing our furniture and doing our architectural installations, doing a lot of work in the super yacht space. And then, the world started to shut down."
Rasmussen said clients sounded the alarm.

"We had four different clients in the medical space all sent us letters saying, 'You're essential and you can't be shutdown.'"
The team quickly found out why.
"What we did is we repurposed our production and tore down machines that were making bracelets and chairs and started making ventilators on the same machines."
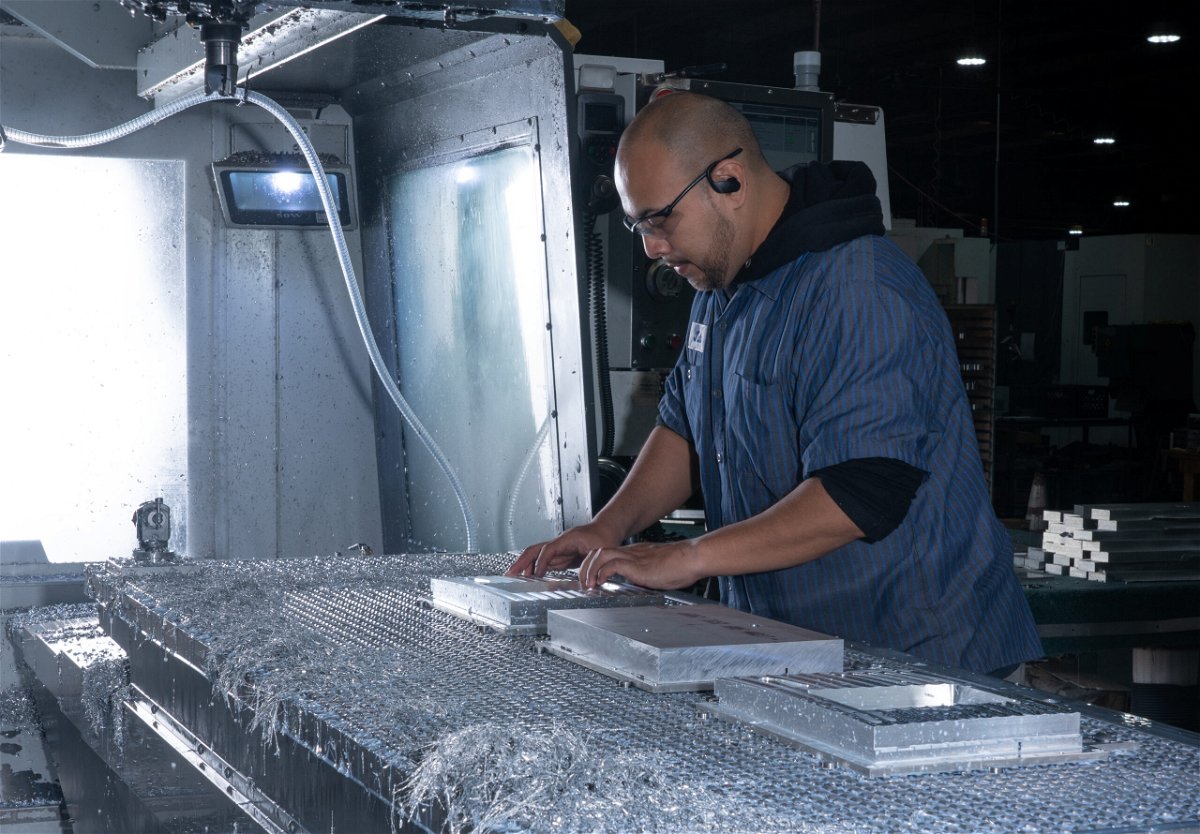
Within days, a huge order came in for the company's coveted thick, anodized aluminum front panels; 2,500 of them. Rasmussen personally delivered the first batch.
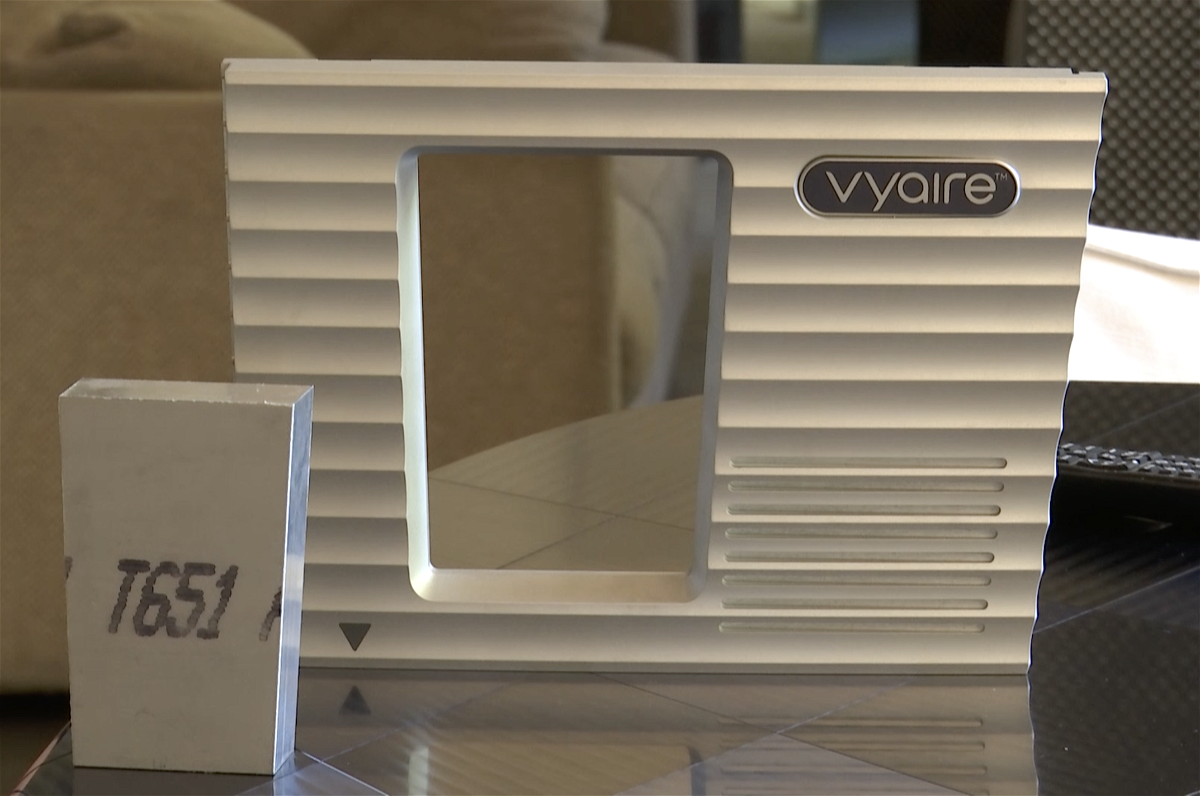
"It was very easy to call all of our customers and say, 'Hey, we can't work on your thing. We got to go make ventilators.'"
The bulk of Neal Feay's sleek retro panels are destined for high-end luxury wi-fi systems; now the vented panels would help save lives.
"We had to move heaven and earth to get the first 50 a day pace going in five days. They said, 'If you can ship more than that, we'll take everything you can ship!' So, we went from 50 a day, four days a week to 75 a day, five days a week."
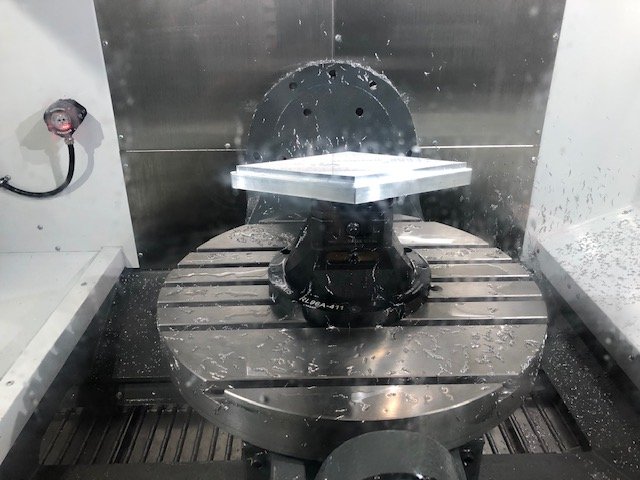
A team of 70 grinding away in 50,000 square feet of working space made it possible to safely churn out the parts. Rasmussen calls their panel a "premium product" not a "commodity ventilator."
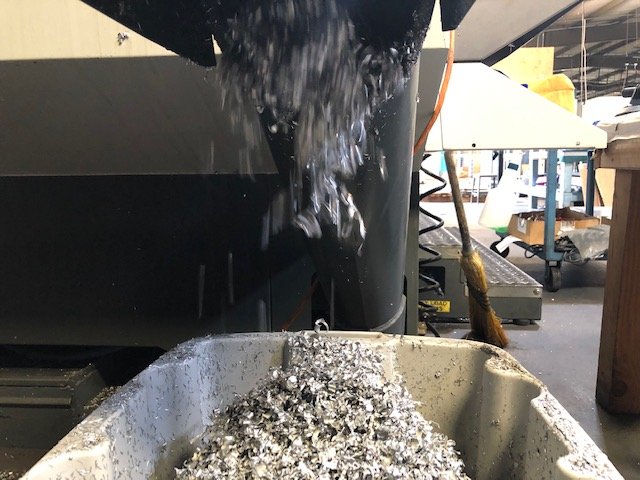
"The one we make actually makes it much easier to keep people alive because it has a lot more feedback to precisely give the right amount of oxygen, not just give oxygen."
Rasmussen is equally proud of his family-run business -- three generations strong -- and his employees, all contributing in the worldwide effort to save lives.
"My team is pretty dear to me and that's probably been, that's been more interesting to me and more motivational to me than making the medical thing pretty. We'll probably be making ventilators for the foreseeable future."
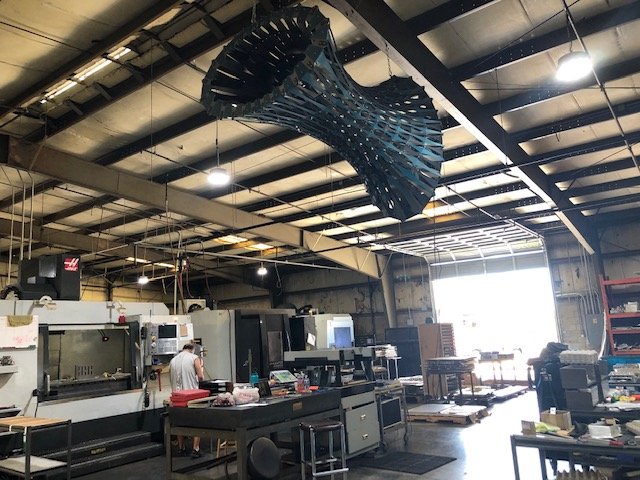
For more information about Neal Feay Co. click the following link: https://www.nealfeay.com